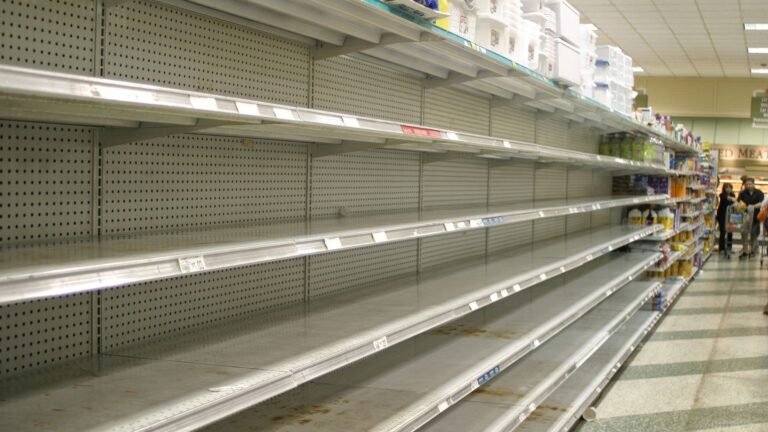
If you ever find yourself in a Recall or Withdrawal situation – are you ready to deal with it?
We help you get ready and have the programs in place to very quickly assess any Food Safety situation and react quickly!
Speed is critical once you hear that you may be in Recall or Withdrawal – are you ready?
We ensure you have an effective Recall Team and Program in place and practiced. Just like a fire-alarm drill.
We review your Mock-Recall exercises and procedure and ensure it’s effective and realistic. I.e. not scheduled, during off-hours and on different materials.
We ensure that you know how to very quickly decide if you are in an actual Recall or Product Withdrawal.
Often, if you move quickly, you can find and secure all the products involved. This reduces your customer impact and your costs, but also reduces regulatory intervention if not a Recall.
As soon as you receive bad micro results, or if you’re in recall or product withdrawal. 📞 Us
We can help you set up an effective Recall Team

All three of the common Hazards (Microbiological, physical, and chemical, including Allergens) can enter your facility from your raw material suppliers. Next to employees and bacterial populations already resident in a facility, suppliers are the most common source. We can help you reduce the risk you inherit when you receive raw materials from your suppliers.
We can visit your raw material supplier’s facilities on-site to confirm that what you buy from them is safe.
We can also help you develop your own “Supplier Approval Program”.
We will tell you where the risk is with your key suppliers, ensuring your facility knows what it is getting.
If you have a new or current supplier with quality issues, we can inspect for you. We can also help with supplier certification for GFSI.